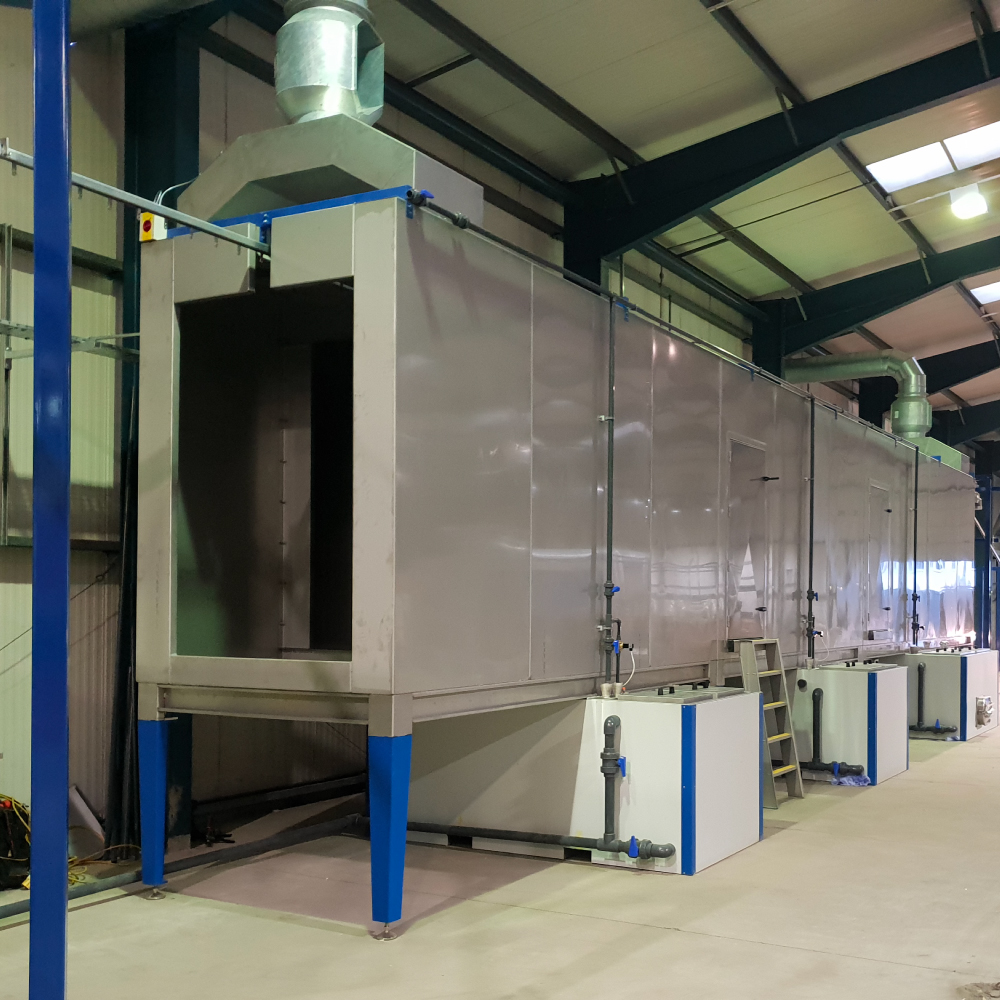
Chemical Spray Pretreatment Systems
Our online chemical spray pretreatment systems are designed to prepare metal surfaces for coating applications by effectively removing contaminants and enhancing adhesion. These systems utilize advanced chemical spray technology to ensure uniform treatment, improving the overall quality and durability of the final finish.
General Specifications
1. System Types
- Quick and straightforward installation process with detailed guides and optional on-site support.
- Compatible with most existing ductwork and systems
2. Pretreatment Process
- Chemical Application: Automated spray application of pretreatment chemicals, including phosphates, rust inhibitors, and cleaners.
- Rinsing: High-pressure rinse system to remove excess chemicals and contaminants.
- Drying: Integrated drying system to ensure surfaces are moisture-free before coating.
3. Dimensions
- All units are Custom sizes – available to fit specific production line requirements.
4. Chemical Storage & Management
- Storage Tanks: Chemical storage tanks made of corrosion-resistant materials with capacities ranging to suit specific plant design.
- Mixing System: Automated chemical mixing and dilution system for consistent application ratios.
5. Spray Application System
- Nozzle Type: High-efficiency spray nozzles designed for even coverage and minimal overspray.
- Pressure Range: Adjustable pressure settings from 30 to 100 psi (2 to 7 bar) for optimal chemical application.
6. Airflow and Ventilation
- Exhaust System: Integrated fume extraction and exhaust fans to maintain a safe working environment.
7. Control System
- User Interface: Touchscreen control panel for easy operation and monitoring of the pretreatment process.
- Features: Programmable cycles, alarms for low chemical levels, and maintenance reminders.
8. Safety Features
- Emergency Stop: Easily accessible emergency shutoff button.
- Chemical Safety: Compliance with OSHA and local safety regulations for chemical handling and storage.
9. Power Requirements
- Electrical: 230v single phase or 415v 3-Phase.
- Air Supply: Minimum pressure requirement of 80 psi for optimal operation.
10. Maintenance
- Access Panels: Designed for easy access to all components for routine maintenance and cleaning.
- Self-Cleaning: Automated cleaning cycles for spray nozzles and lines to prevent clogging.
Additional Options
- Custom Chemical Formulations: Ability to accommodate various pretreatment chemicals based on specific customer needs.
- Temperature Control: Optional heating elements to optimize chemical performance in colder environments.
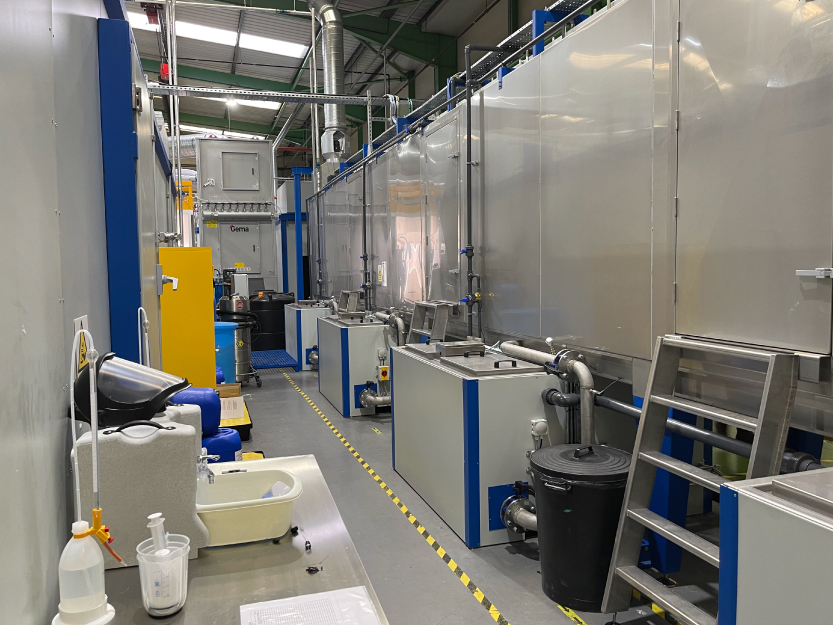
Warranty and Support
- Warranty: 1-year limited warranty on all parts.
- Customer Support: Technical support and assistance with installation and maintenance.
Conclusion
Our online chemical spray pretreatment systems are designed to enhance the surface preparation process, ensuring optimal adhesion and finish quality for coatings. With advanced technology and customizable options, these systems are the ideal solution for manufacturers seeking efficiency and reliability in their pretreatment processes.
For further information or to discuss specific requirements, please contact our sales team or visit our website.